Modern production control software to maximize efficiency
GE Vernova’s Plant Applications is an effective operative control solution for process-based, hybrid and discreet producers, for example in the production of food and drink products, packaged consumer goods and electronic devices. The solution helps to manage strongly automated, swift processes by data collection and analysis.
Plant Applications has been one of the leaders in the field of Manufacturing Execution Systems (MES) already for two decades and it automatizes and integrates information related procedures for production execution and performance optimization. It helps to maintain the balance of the competing priorities of production processes to ensure maximum efficiency and profitability.
Results
• Increased operation efficiency by providing information on the efficiency of individual devices
• Functions specifically designed to solve challenges provide an overall improvement of manufacturing performance
• Visualization, analysis, optimization and execution functions improve accuracy
• Provides uncompromised quality using a combination of GE Six Sigma and Lean methodologies and its own production processes
• Implementation time can be shortened by using commercial off-the-shelf software (COTS) that offers quicker deployment.
Efficiency management
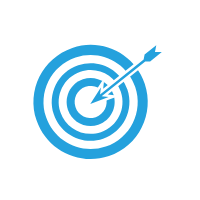
Efficiency management tracks and monitors overall equipment effectiveness (OEE) and other KPIs, downtime, number of defects and produced quantity, mean time between failures (MTBF), mean time to repair (MTTR) and so on.
- Events are automatically or manually assigned to causes and made ready for root cause analysis.
- Data can be summarized and analysed based on context.
- Events and causes can be matched to actual production parameters. Standard and ad hoc reports and dashboards can be used to assist real time decisions.
Production control
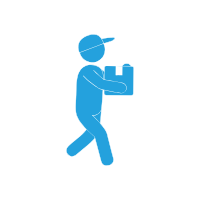
Used to define and manage the optimal path and operations to manufacture a specific product on a specific production line. Production control manages production operations, including the product flow between machines, the genealogical connections of the product and any scheduling changes to optimize stocks. It employs an efficiency-centred method to support the execution of the production schedule and product tracking in comparison with the predefined deadlines. Production control supports comprehensive tracking of individual products at each step of the manufacturing process and enables the generation of audit quality genealogy and production reports.
Quality control
.png)
Quality control ensures a consistent level of quality. It provides real time trends, statistics and notifications to control quality levels, keeping up with the pace of your company. It integrates process, inspection and test data from manual or automatic sources and stores this information in one, integrated store. Furthermore, quality control links operator notes, specifications, recipes and procedure documents to this information.
Plant Applications helps to understand operational performance. It provides simplified visualizations to increase operator productivity.
Batch analysis
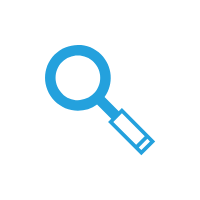
A unique, multi-level approach and standard, commercially available Batch Control interface facilitates connecting to both new and legacy systems. It provides features to analyse scheduled and finished lots and generates an electronic batch record to improve product quality and consistency.
Product features
- Clearly displays the main areas and reasons for production losses, for example faults, defects and downtime
- Common MES platform for multimodal production – continuous, discreet, and hybrid production
- Raw production data is converted to automatically monitored and consistently managed performance metrics
- Uses the best practices of world leading companies in performance control
- Standards-based (S95) unified production database
- Replaces manual data collection and logging
- Comprehensive reporting and analysis tools help to identify issues and execute performance enhancing activities
- Service-oriented architecture to implement a less complicated connection between systems that enables more expedite solution development and deployment
- User friendly interfaces with modular features designed for future growth
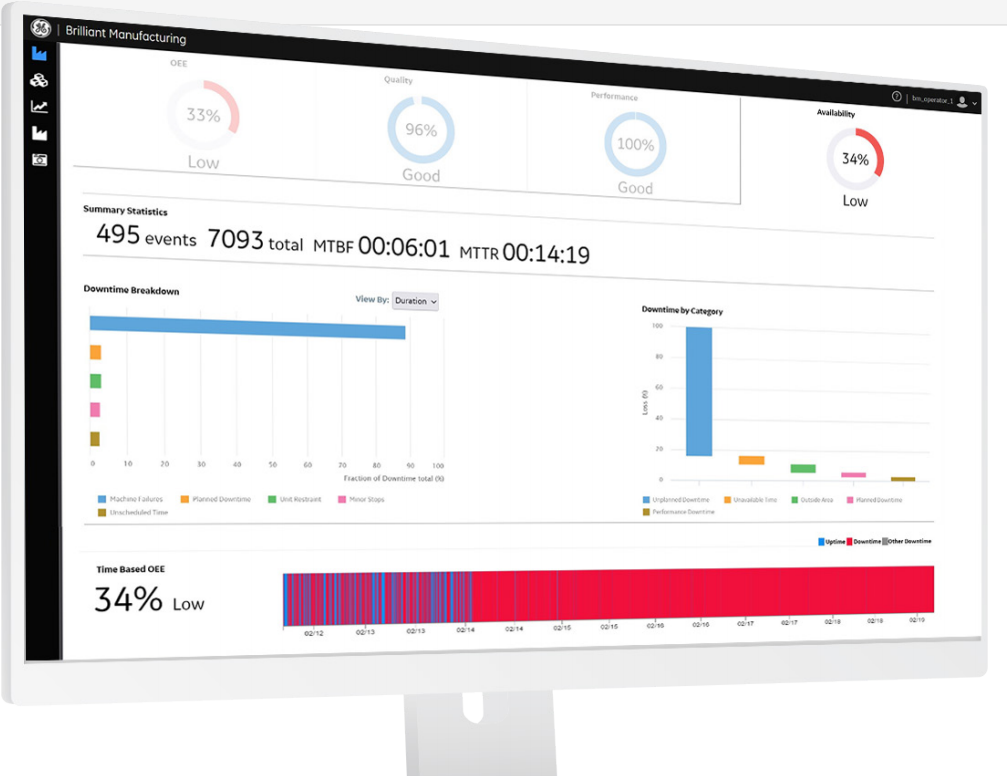
Hardware requirements
The minimum server system requirements for running the Plant Applications platform are as follows:
- 4 cores CPU, 3 GHz
- 8 GB RAM
- 500 GB disk space
The following specification is recommended for normal implementations:
- 8 cores CPU
- 16 GB RAM
- 1 TB
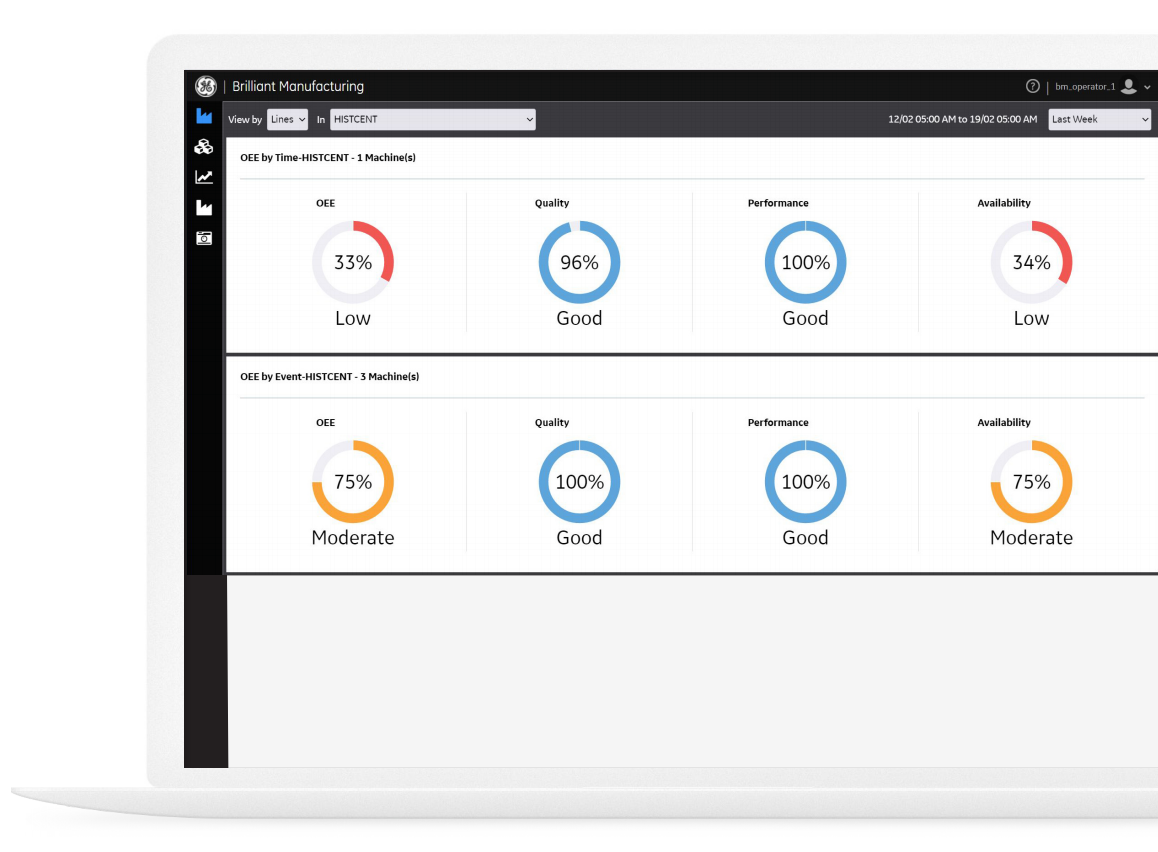
Software requirements
- Windows Server 2012 R2, 2014 or 2016 for server installations (32- or 64-bit)
- Windows 7 for client installation (32- or 64-bit)
- SQL Server 2012, 2014 or 2016 (32- or 64-bit)
- Web Server IIS 7.0 or later, OS dependent
- Microsoft .NET Framework 4.5
- Microsoft Excel 2013 or 2016
- Browsers
- Microsoft Internet Explorer 11 (web reports)
- Chrome v56.0+ (Universal Client)
- Safari v10.0+ (Universal Client)
- PDF reader (required to display certain web reports)
- GE Digital Workflow browser (32-bit version)
- GE Digital Historian 7 browser (to use Universal Client)
Get to know how Plant Applications helps to make optimal decisions regarding the competing priorities of production to maximize operational efficiency.
Plant Applications provides detailed information with just a few clicks to facilitate quicker and more informed decisions.
You may also be interested in the following
How can Com-Forth help?
Following and initial assessment, Com-Forth can provide assistance in the following areas:
- map existing systems, equipment and processes
- assess requirements by user groups (consultation, workshop, verbal audit involving the affected groups including management, production, engineering, quality assurance, maintenance, IT, HR and so on)
- create a concept plan and roadmap with milestones and deadlines
REQUEST INFORMATION
Zoltán Tőkey senior software consultant has been a key member of the Com-Forth team since 2003. He created several MES systems and our proprietary ERP system.
Com-Forth needs the contact information you provide to us to contact you about our products and services. You may unsubscribe from these communications at any time. For information on how to unsubscribe, as well as our privacy practices and commitment to protecting your privacy, please review our Privacy Policy.